Process optimisation and simulation
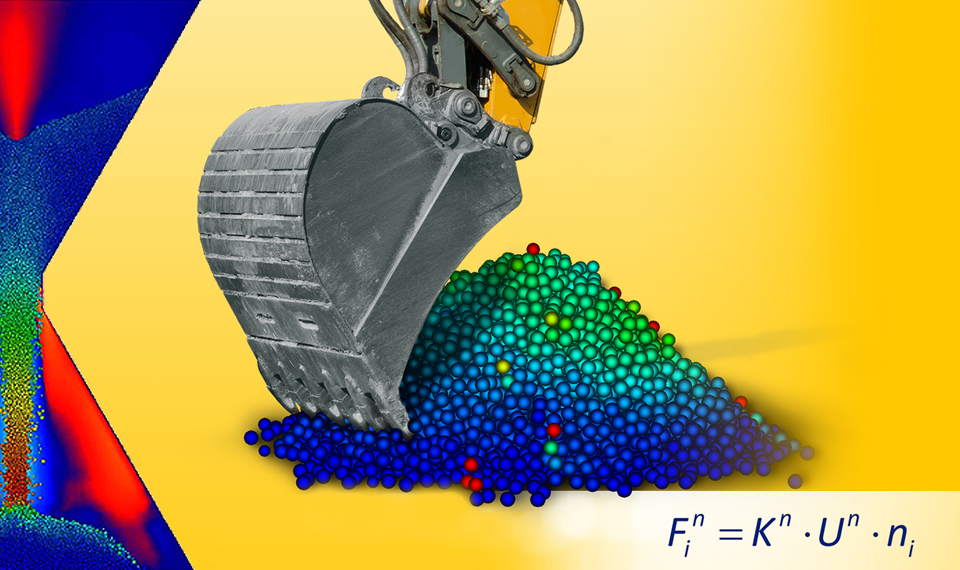
Process simulation or visualisation alone is never going to be our end goal. Rather, our aim is always to develop a comprehensive understanding of the entire process and system architecture.
IBAF supports manufacturers of machines and mobile plant in the planning, implementation and optimisation of the associated operational processes.
Analysis and optimisation of mobile plant processes
The expert analysis of relevant documents and inspection of a system can often be sufficient for achieving a good initial understanding of the technology concerned and proposal of optimisation measures. Conversely, the measurement of process variables in digging, crushing, compaction, materials handling and other mobile plant processes can often present considerable difficulties. IBAF therefore analyses such processes with the aid of the Discrete Element Method (DEM) using graphic 3D simulation technology. This enables the quantification of internal process forces and velocities, providing a basis for determining losses and efficiencies, tribological stresses or dust generation. Where necessary, machine models (MBS) or flows (CFD) are also taken into account.
Typical areas of application
- Digging processes and shovel- or bucket-fill optimisation
- Crushing processes and penetration optimisation
- Compaction processes with cohesive materials such as asphalt
- Optimisation of handling capacity within a machine •Mixing and grinding processes
- Exhaust and cooling systems
DEM, CFD or coupled simulations create a system understanding and thus a sound basis for targeted optimisation and further development activities. New conceptual ideas can be verified and key parameters defined for variant comparisons.
Simulation know-how for your process
Material parameterisation – The quality of simulation results depends decisively on the selected boundary conditions and material parameters. The material spectrum ranges from fine dusts to rock for crushing, the range of applications from small loader to semi-mobile crusher.
IBAF has extensive experience and the necessary experimental equipment to parameterise free-flowing, granulated, cohesive or monolithic materials. From simple slump and pouring tests to fracture tests, by comparing real and virtual test results, the parameters appropriate to the actual, complex process simulation are determined iteratively. In this way, simulation results are generated that reliably map the actual system behaviour.
Coupled simulations – IBAF performs coupled simulations where the boundary conditions are more complex and the material flow interacts with other physical variables. Coupling will usually involve combinations of the following systems:
- Discrete Element Method (DEM)
- Computational Fluid Dynamics (CFD)
- Multi-Body Simulation (MBS)
- Finite Element Method (FEM)