Vibration analysis and engineering acoustics
Beyond performing acoustic analyses on machinery and systems, we are also committed to developing specific measures to reduce vibration and noise.
IBAF supports manufacturers and operators of machines, vehicles and mobile plant as well as their component suppliers in the reduction of vibrations and noise from initial concepting phase through to commercialisation. We cover everything from rapid problem-solving and solution implementation to the targeted development of low-vibration and low-noise systems. We can be relied upon to select the appropriate measurement or simulation method for analysis and evaluation of the causes, transmission paths, emissions and immissions (perceived effects) of vibrations in all frequency ranges.
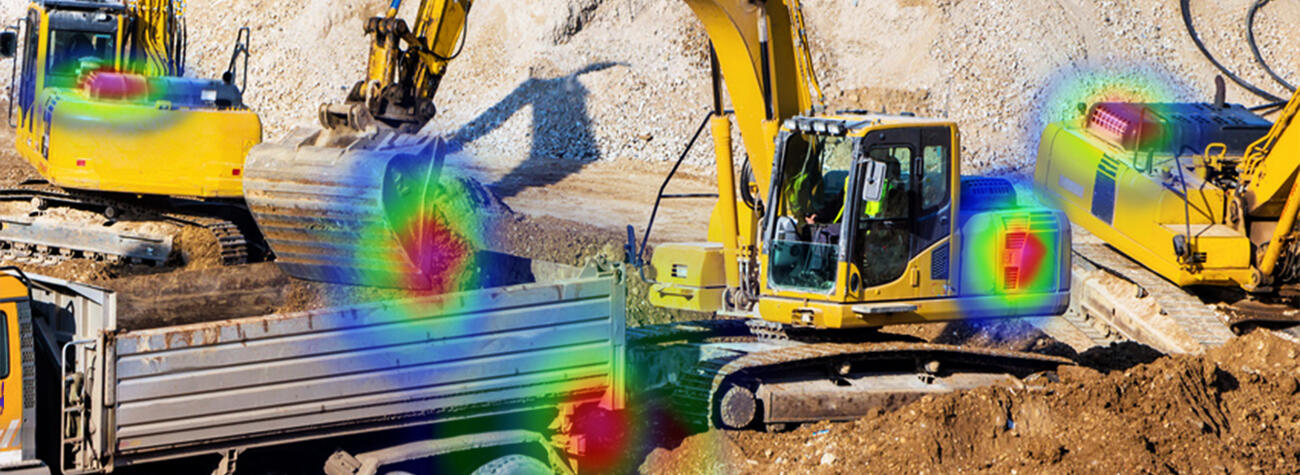
Vibroacoustic problem-solving
- Functionally relevant vibration and shock loading
- Strength-relevant vibration
- Vibration exposure of employees
- Cause, transfer and radiation of noise
- Solutions to nuisance problems
Testing and measurement techniques for accurate vibroacoustic system analysis
We aim to provide a thorough understanding of the vibration or acoustic system on the basis of competently planned and executed tests and metrological analysis as a necessary basis for specific optimisation measures.
- Measurement of acceleration, stress and deformation; determination of vibration velocities and paths
- Sound pressure measurements with single microphones and acoustic cameras, determination of sound power level spectra
- Fourier analysis of the time signals to identify relevant frequency ranges
- Exciter identification and transfer path analysis
Experimental modal analysis Shock measurements are becoming increasingly important for the quantification of, for example, the loads affecting electronic components. Hence we offer the following:
- Acceleration measurements
- Peak identification and classification, measurement of duration and amplitude
- Definition of (test) specifications for relevant components
Simulation as the basis for understanding vibration systems
Simulation of dynamic system behaviour and noise propagation allows systematic analysis of relevant parameters and variables. The resultant in-depth understanding of the system not only facilitates accurate determination of optimisation concepts but also reliable estimation of their potential.
- Modal analyses (Matrix Structural Analysis, FE, MBS) for determining natural (eigen) frequencies and natural modes
- Frequency response analyses (FE, MBS) for quantification of system response to a given excitation
- Torsional vibrational analyses for drive systems
- Multi-body simulation (MBS) for assessment of the dynamic behaviour of integrated systems
- Calculation of the radiated sound field (BEM)
- Noise predictions / charting
Problem-aligned solutions
Whether supported by comparative simulations or based on prototype testing with validated measurement data, we invariably find a solution to your problem.
- Detuning of systems in the critical frequency range
- Selection of suitable damping elements and vibration absorber masses, elastic decoupling measures
- Interruption of transmission paths and transfer path modification
- De-excitation, for example through optimisation of drive characteristics
- Silencers, mufflers and sound absorbers, enclosures, hoods, screens, linings, covers and walls
- Sound masking solutions