Chassis and drive technology
When it comes to component design, accuracy and precision are paramount. The aim has to be solutions that are fully standard- and approval-compliant with verification aligned to the specific operating conditions of the railway concerned.
And it is the wheel-rail system that literally gets trains and other rail vehicles rolling. IBAF supports vehicle and component manufacturers in the development and verification of the corresponding safety-relevant system components and the key elements of the upstream powertrain.
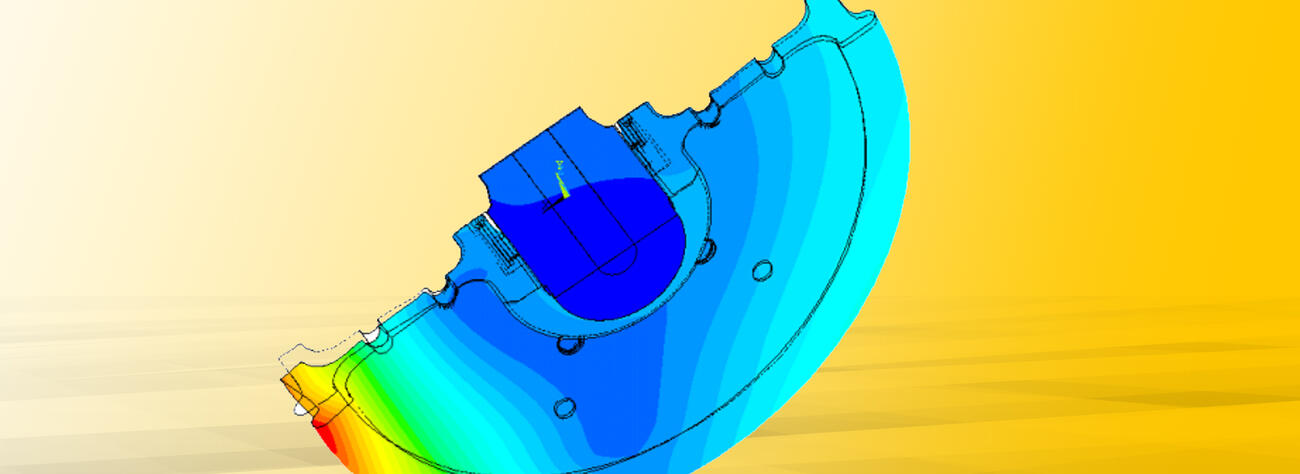
Fatigue analyses and strength assessments of train wheels and axles
Even the simple forged wheel body with press-formed bore requires a special procedure for its fatigue strength analysis under rotation. Elastic intermediate layers and thermal stresses from block brakes further increase the demands on the calculation models for e.g.:
- Monobloc wheels
- Steel-tyred wheels
- Resilient (rubbersprung) wheels
IBAF offers extensive experience in the integration of multiphysics elements, nonlinear material behaviour (hyperelastic, plastic), major deformation behaviour and high-accuracy substitution modelling for the verification process.
In order to effectively cover the entire spectrum of requirements and to meet the high safety standards imposed, we use our own algorithmic evaluation tools, applying full-scope verification to each node of the assembly in question, e.g. according to UIC 510-5 / EN 13979-1 and UIC 810-1V.
Dynamic drive train simulation and component engineering
A component, such as a train gearbox, should be considered as part of the overall powertrain system, taking into account the specific installation situation in the vehicle concerned.
Accordingly, the dynamic system behaviour is determined on the basis of a dynamic simulation of the entire integrated system, including real driving profile computation, with the data then being appropriately used for component design. Similarly, connection stiffnesses and transfer paths are considered for the strength, deformation and structural vibration assessments.
Our algorithmic evaluation tools allow rapid assessment of components and assemblies in accordance with current standards and codes of practice (e.g. FKM guideline for analytical strength assessment of mechanical components, German standard VDI 2230). If the vibroacoustic behaviour is critical, modal and frequency response analyses as well as structure-borne sound calculations can also be integrated within the overall appraisal.